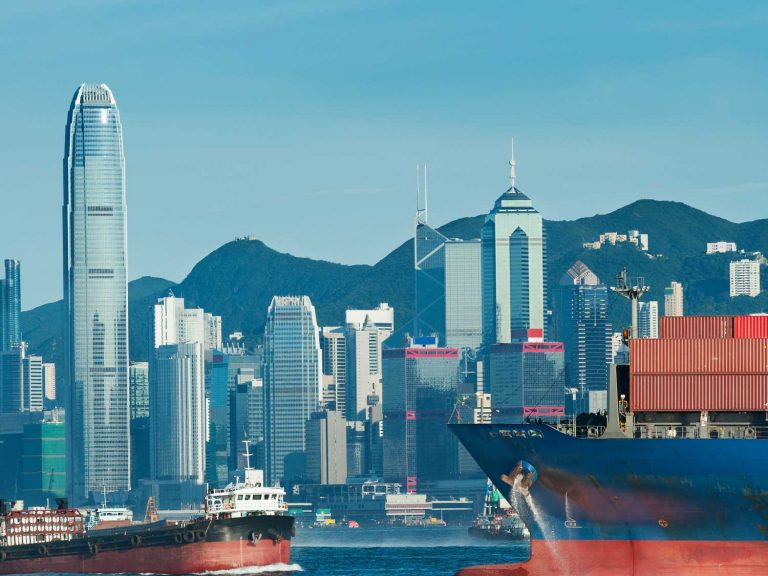
Date:
Ocean Freight Update; On the front line from Asia
Our sea freight ops team continue to perform in a very challenging global ocean freight environment and with global supply chains likely to be under pressure for the rest of the year, they will continue to deliver the highest possible levels of service and performance available with all options being considered. Overcoming operational impacts and dealing with issues, which are often due to circumstances beyond their control, and protecting their customers.
We highlight the current situation and our review of running global sea freight operations in 2021.
During the first two months of 2021, while the market experienced severe equipment shortages, incredibly, vessels started to depart Asia at less than capacity.
This was the direct result of a substantial lack of equipment of all types being available to load, in the areas where they were needed.
The lines’ immediate actions included moving empty containers, instead of laden exports from key markets such as Europe and the Americas, in order to turn the equipment around more quickly back to Asia. However, due to congested ports, caused in the main by a slowdown in operations having to adopt Covid restrictive processes and unreliable vessel schedules missing berthing slots, which in turn contributed to port congestion and further transit delays, empty containers have largely remained stuck across the world, in places where they are not needed.
As we started Q1 the general consensus of the shipping lines was that issues of equipment and space would start to ease and then continue to improve as we entered Chinese New Year and beyond.
Now all factories are back up and running and demand returned to the same level as December/January by Week 10/11 and is forecast to continue into Late Q2. We will then essentially enter the traditional Peak Season for Q3 and the carriers do not expect a demand slow down until potentially the end of Q4.
Global schedule reliability dropped to below 35% in January 2021 – barely half its level last year, which was considered unacceptable by most shippers – and continued its dismal progress to the lowest levels since records began over 10 years ago and this was BEFORE the Suez blockage, which has exasperated the situation leading to further schedule delays and impacting equipment availability globally.
The week-long Suez closure has resulted in many delays enroute, including, but not exclusively, to late arrivals, port omissions and delays to arrivals of anything up to four weeks after shipment from origin.
The carriers are maintaining their peak season charges throughout Q2, and market rates remain very high for both contract renewals and in the spot market, which is forecast to continue throughout 2021.
With continued widespread port congestion and carriers still not able to add sufficient capacity, we might not see improving schedule reliability until Q3/Q4 of 2021 or even later.
All the above results in difficulty obtaining vessel space and equipment as required and therefore makes planning, communication and co-operation more important than ever. Proactive visibility remains an essential ingredient to managing the current market conditions.
The market was already working hand-to-mouth for equipment and now with the added pressure of the Suez incident, the Far East Region is 600,000TEU short of equipment versus current requirements, which represent the capacity caught up in the subsequent vessel delays arriving later than planned in the Far East.
The four weeks’ notice we request for bookings is to ensure that we secure and allocate space on the vessel, because we cannot reserve or pre-book equipment with most carriers as per their processes in a shorter time period.
We secure space and equipment with all carriers, across all POL’s (port of loading) which is subject to release at the time the EIR is applied for (which your shipper does) on a case by case basis based on what is in the empty container depot at that exact time.
As an example ex Ningbo the market is almost 8000TEU short for planned bookings for next week alone across all carriers and markets.
Unfortunately no carrier will reserve equipment in advance or allow equipment to be stockpiled for future bookings, as demand totally outstrips the supply, and every container is required for immediate bookings in the current environment.
Carriers will only look to release equipment once the vessel has opened, which is usually 5-7 days before the planned sailing date.
The shippers need to be applying for EIR’s as soon as they can and keep applying until successful, they also need to keep our origin partners updated if they experience any issues with that so we can try and intervene on their behalf. With many carriers now if we cancel a booking within the 2 week window of sailing then we face a heavy penalty charge despite the lack of equipment so pre-planning is paramount and early visibility of all movements to ensure that containers are loaded on intended vessels.
For further information please contact you daily account team or Emma Hulbert for any clarification. Hopefully the situation will improve over coming weeks and months and we will continue to update the situation regularly as it changes.